Ribbon Blender Machine
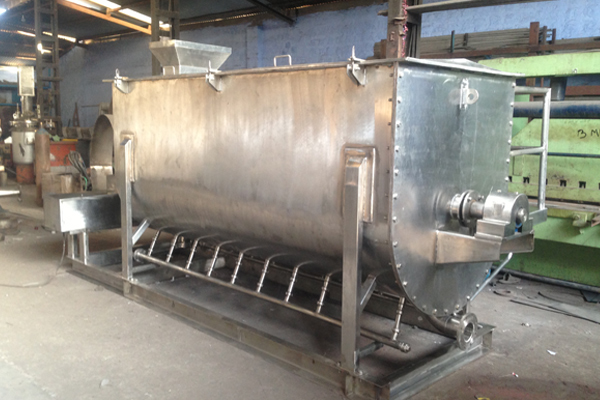
We are then backed with the rich industrial experience in the field of manufacturing, supplying and exporting Ribbon Blenders. Our provided Ribbon Blenders are manufactured using materials of stainless steel or mild steel with various other components. The process of our inner ribbon constantly circulates the material and outer ribbon moves the ingredients in the blender. Moreover, ends of the vessel are provided with stuffing boxes on the shaft diameter. This stuffing box prevents leakage of material and also prevents material from entering into the bearings. The shaft is supported on heavy duty pedestals. The mixer is offered with a hopper and discharge. The drive consists of a suitable gear box coupled to the motor.